Renault Clio: Injector rail: Removal - Refitting
K9K, and 764 or 772
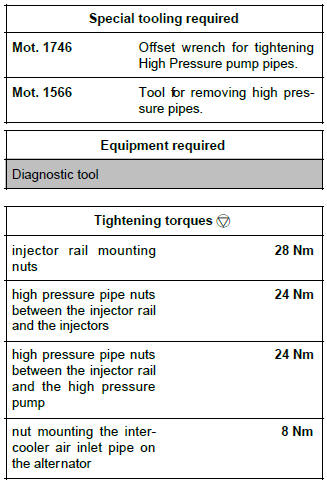
WARNING
Before starting work on the vehicle, have to hand:
- a new blanking plug kit (part no. 77 01 476 857),
- cleaning wipes (part no. 77 11 211 707),
- cleaning product (part no. 77 11 224 188).
WARNING
Parts always to be replaced:
- all the high pressure pipes which have been
removed.
REMOVAL
I - REMOVAL PREPARATION OPERATION
- Position the vehicle on a lift (see Vehicle: Towing
and lifting) (MR 392, 02A, Lifting equipment).
- Switch off the ignition and wait 30 seconds before
starting work on the injection system.
IMPORTANT
Before carrying out any work on the injection system,
check using the Diagnostic tool :
- that the rail is not under pressure,
- that the fuel temperature is not too high.
It is essential to respect the safety and cleanliness advice whenever
work is carried out on this system (see 13B, Diesel injection, Diesel injection:
Precautions for the repair, 13B-1).
- Disconnect the battery (see Battery: Removal - Refitting)
(MR 392, 80A, Battery).
- Remove the engine cover.
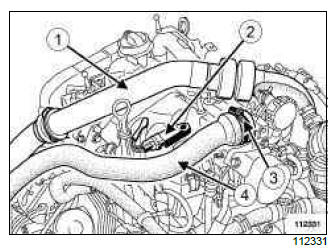
- Remove the upper section (1) of the turbocharging
duct.
- Disconnect the inlet air pressure sensor (2)
- Loosen the clip (3).
- Move the inlet duct to one side (4).
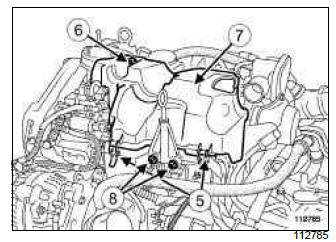
- Unclip the clips (5) from the injector rail protector
cover.
- Remove:
- the injector rail protector cover mounting bolt (6),
- the injection rail protector cover (7),
- the dipstick,
- the dipstick tube (8) mounting bolts.
- Move the dipstick duct to one side.
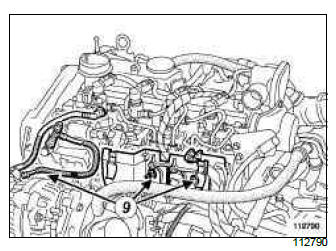
- Remove:
- the injector rail protector support mounting bolts (9),
- the injector rail protector mounting.
- Protect the alternator from fuel outflow.
- Pour cleaning product into a container.
IMPORTANT
Wear protective gloves when using cleaning
product.
- Soak the brush with cleaning product, then clean the
unions:
- of the high pressure pipes between the injector rail
and the injectors
- of the high pressure pipe between the pump and
the injection rail.
- Blast the cleaned areas with compressed air, then
wipe them with new cleaning cloths.
IMPORTANT
Wear protective glasses.
WARNING
Do not blow compressed air once the fuel circuit
is open, otherwise impurities may enter the system.
Use wipes if necessary.
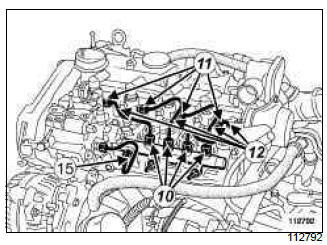
- Undo:
- the nut securing the four high pressure pipes between the injection
rail and the injector at the rail end (10),
- the nut securing the high pressure pipes between the injection rail
and the injector at the injector end (11),
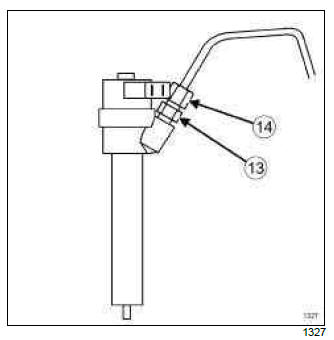
WARNING
When the high pressure pipe unions (14) on the
injector holder have been loosened, always hold
the rod filter retaining nut (13) with a lock wrench.
- Remove the four high pressure pipes (12) and discard
them.
Note:
Make preparations for fuel outflow. Clean with
new cloths.
- Fit the blanking plugs.
- Remove the high pressure pipe between the high
pressure pump and the injection rail and discard it.
Note:
Hold the intermediate nut between the pump-rail
pipe and the high pressure pump using a lock
wrench.
Note:
Make preparations for fuel outflow. Clean with
new cloths.
Insert the correct blanking plugs.
II - REMOVAL OF PART CONCERNED
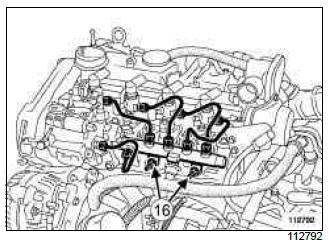
- Remove:
- the injector rail mounting nuts (16),
- the injector rail.
WARNING
If the injection rail is to be reused, keep it in a
sealed plastic bag all the time it is disconnected.
REFITTING
I - REFITTING PREPARATION OPERATION
WARNING
Remove the blanking plugs only before reconnecting
the fuel circuit pipes.
The plugs are single-use only. Do not reuse
them, and discard the kit once opened.
- Take the injector rail out of its plastic bag
WARNING
If an injector rail is being replaced, only remove
the new one from its original packaging when it is
about to be fitted.
II - REFITTING PART CONCERNED
- Fit the injector rail.
- Finger tighten the injection rail mounting bolts (the
injection rail should be loose).
III - FINAL OPERATION.
- Remove the blanking plugs from:
- the high pressure pump,
- the injection rail fuel inlet opening.
- Fit a new high pressure pipe between the injector rail
and the high pressure pump.
Note:
If the new pipe kit does not contain an applicator,
lubrication of the pipe threads will be unnecessary
(as they are self-lubricating pipes).
- Finger tighten the high pressure pipe nuts until they
make contact.
- Remove the blanking plugs from:
- the rail injector fuel return openings,
- the injector fuel inlet.
- Fit the new high pressure pipes between the rail and
the injectors.
Note:
If the new pipe kit does not contain an applicator,
lubrication of the pipe threads will be unnecessary
(as they are self-lubricating pipes).
- Finger tighten the high pressure pipe nuts until they
make contact.
- Torque tighten:
- Refit:
- the injector rail protector mounting,
- the mounting bolts from the injection rail protector
mounting,
- the dipstick duct mounting bolts.
- the dipstick,
- the injector rail protector cover,
- injection rail protector cover mounting bolts,
- Refit the air inlet duct and tighten the mounting clip.
- Connect the inlet air pressure sensor
- Loosen the mounting nut securing the intercooler
air inlet pipe to the alternator,
- fit the air duct between the turbocharger and the intercooler
air inlet pipe,
- lock the air duct onto the turbocharger and the intercooler
air inlet pipe.
- tighten the air duct bolt on the rocker cover,
- torque tighten the nut mounting the intercooler
air inlet pipe on the alternator (8 Nm).
- Reprime the fuel circuit.
- Connect the battery (see Battery: Removal - Refitting)
(MR 392, 80A, Battery).
- Confirm that there is no diesel fuel leak:
- check the sealing after repair (see 13B, Diesel injection, High
pressure pipe: Check, 13B- 99),
- let the engine run at idle speed until the engine
cooling fan starts to operate,
- accelerate several times at no load,
- check that there are no diesel leaks.
- Use the Diagnostic tool to check for stored faults.
Clear them if necessary.
K9K, and 750 or 752 or 766 or 768
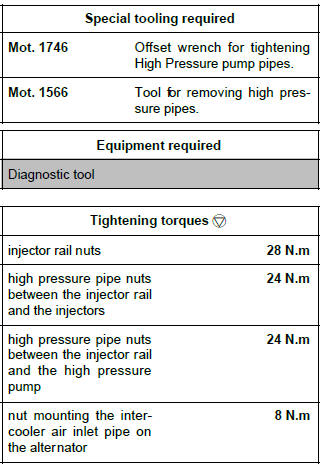
WARNING
Before starting work on the vehicle, have to hand:
- a new blanking plug kit (part no. 77 01 206 804),
- cleaning cloths (part no. 77 11 211 707),
- cleaning product (part no. 77 11 224 188).
WARNING
Parts always to be replaced:
- all the high pressure pipes which have been
removed.
Note:
Vehicles equipped with the K9K*768 engine may or
may not be equipped with an intercooler.
REMOVAL
I - REMOVAL PREPARATION OPERATION
- Position the vehicle on a lift (see Vehicle: Towing
and lifting) (MR 392, 02A, Lifting equipment).
- Switch off the ignition and wait 30 seconds before
starting work on the injection system.
IMPORTANT
Before carrying out any work on the injection system,
check using the Diagnostic tool :
- that the rail is not under pressure,
- that the fuel temperature is not too high.
It is essential to respect the safety and cleanliness advice whenever
work is carried out on this system (see 13B, Diesel injection, Diesel injection:
Precautions for the repair, 13B-1).
- Disconnect the battery (see Battery: Removal - Refitting)
(MR 392, 80A, Battery).
- Remove the front engine cover.
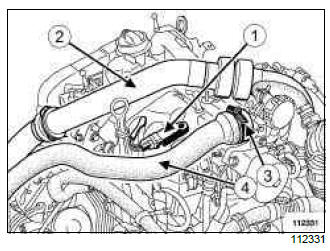
- Disconnect the inlet air pressure sensor (1).
K9K, and 750 or 766 or 768
- Remove the upper section (2) of the turbocharging
duct.
- Loosen the clip (3).
- Move the inlet duct to one side (4).
- Remove:
- the dipstick,
- the dipstick duct bolts.
- Move the dipstick duct to one side.
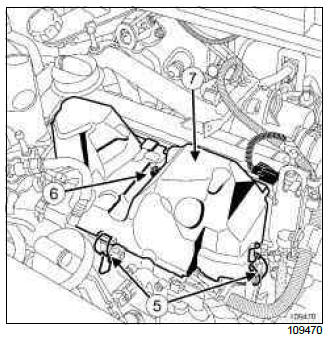
- Unclip the clips (5) from the injector rail protector
cover.
- Remove:
- the injector rail protector cover bolt (6),
- the injector rail protector cover (7),
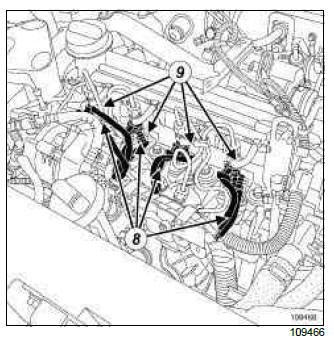
- Disconnect the connectors from the injectors (8) and the heater plugs
(9).
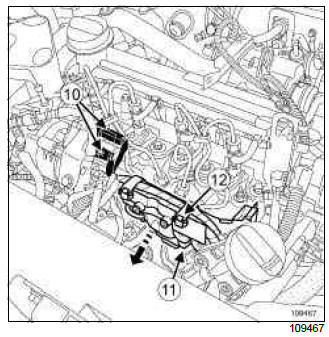
- Disconnect:
- the connectors (10) from the fuel flow actuator and
the diesel temperature sensor,
- the pressure sensor (11) from the spherical injector
rail,
- Move the electric wiring harness and neck to the
side as shown by the arrow.
- Remove the mountings from the neck (12) fixed on
the spherical rail.
- Protect the alternator from fuel outflow.
- Pour cleaning product into a container.
IMPORTANT
Wear protective gloves when using cleaning
product.
- Soak the brush with cleaning product, then clean the
unions:
- on the high-pressure pipes between the injector rail
and the injectors,
- of the high pressure pipe between the pump and
the injection rail.
- Blast the cleaned areas with compressed air, then
wipe them with new cleaning cloths.
IMPORTANT
Wear protective glasses.
WARNING
To prevent impurities from entering, once the fuel
circuit is opened, it must not be blasted with compressed
air. Use cloths if necessary.
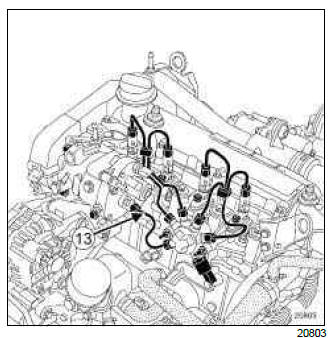
- Remove the clips between the high pressure pipes.
- Undo:
- the nut securing the high pressure pipes between
the injection rail and the injector,
- Remove the four high pressure pipes and discard.
Note:
Make preparations for fuel outflow. Clean with
new cloths.
- Insert the blanking plugs.
- Remove the high pressure pipe between the high pressure pump and the
injector rail (13).
Note:
Make preparations for fuel outflow. Clean with
new cloths.
- Insert the blanking plugs.
II - REMOVAL OF PART CONCERNED
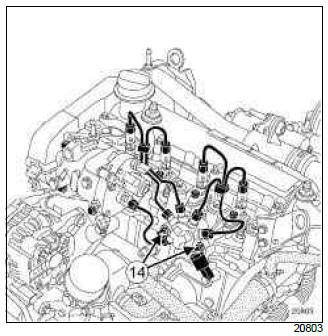
- Remove:
- the nuts (14) from the injector rail,
- the injector rail.
WARNING
If the injector rail is to be reused, keep it in a
sealed plastic bag all the time it is disconnected.
REFITTING
I - REFITTING PREPARATION OPERATION
WARNING
Only remove the blanking plugs immediately
before connecting the fuel circuit pipes.
The plugs are single-use. Do not reuse them,
and discard the whole kit once opened.
- Take the injector rail out of its plastic bag.
WARNING
If an injector rail is being replaced, only remove
the new one from its original packaging when it is
about to be fitted.
II - REFITTING PART CONCERNED
- Fit the injector rail.
- Screw on the injector rail bolts without tightening
them (the rail should be loose).
III - FINAL OPERATION
- Remove the blanking plugs from:
- the high pressure pump,
- from the fuel inlet port of the injector rail.
- Fit a new high-pressure pipe between the injection
rail and the high-pressure pump.
Note:
If the new pipe kit does not contain an applicator,
lubrication of the pipe threads will be unnecessary
(as they are self-lubricating pipes).
- Screw on the high pressure pipe nuts by hand until
contact is made, but without tightening them.
- Remove the blanking plugs from:
- from the fuel outlet ports of the injector rail,
- from the fuel inlet of the injector.
- Fit the new high-pressure pipes between the rail and
the injectors.
Note:
If the new pipe kit does not contain an applicator,
lubrication of the pipe threads will be unnecessary
(as they are self-lubricating pipes).
- Screw on the high pressure pipe nuts by hand until
contact is made, but without tightening them.
- Torque tighten:
- the injector rail nuts (28 N.m),
- the high pressure pipe nuts between the injector
rail and the injectors (24 N.m) using the (Mot.1746) or (Mot. 1566), starting on the injector side,
- the high pressure pipe nuts between the injector
rail and the high pressure pump (24 N.m) using
the (Mot. 1746) or (Mot. 1566), starting on the
high pressure pump side.
- Refit:
- the wiring harness with the neck,
- the channel mountings,
- the dipstick duct bolts,
- the dipstick,
- the injector rail protector cover,
- the injector rail protector cover bolt.
- Connect the electrical connectors.
- Refit the air inlet duct and tighten the mounting clip.
- Connect the inlet air pressure sensor.
K9K, and 750 or 766 or 768
- Loosen the intercooler inlet air pipe nut on the alternator.
- Fit the air duct between the turbocharger and the intercooler
inlet air pipe.
- Lock the air duct onto the turbocharger and the intercooler
inlet air pipe.
- Tighten the bolt of the air duct on the rocker cover.
- Torque tighten the nut mounting the intercooler
air inlet pipe on the alternator (8 N.m).
- Re-prime the fuel circuit.
- Connect the battery (see Battery: Removal - Refitting)
(MR 392, 80A, Battery).
- Check that there are no diesel leaks:
- check the sealing after repair (see 13B, Diesel injection, High
pressure pipe: Check, 13B- 99),
- let the engine run at idle speed until the engine
cooling fan starts to operate,
- accelerate several times at no load,
- check that there are no diesel leaks.
- Use the Diagnostic tool to check for stored faults.
Clear them if necessary.
Rail pressure sensor: Removal - Refitting
K9K, and 764 or 772
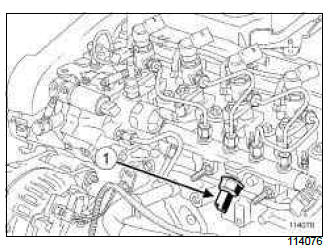
The injector rail pressure sensor (1) cannot be separated
from the injector rail.
In the event of a fault on the rail pressure sensor, replace the "rail pressure
sensor - injector rail and high pressure pipes" assembly (see 13B, Diesel
injection, Injector rail: Removal - Refitting, 13B-64).
K9K, and 750 or 752 or 766 or 768
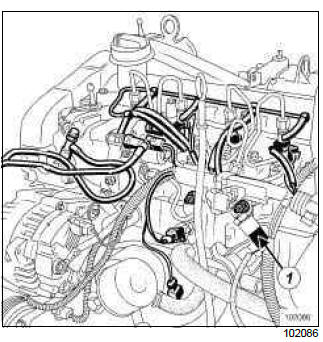
- The pressure sensor (1) cannot be removed from
the spherical injector rail.
If the pressure sensor is faulty, replace the " pressure sensor - high
pressure pipes and rail " assembly (see 13B, Diesel injection, Injector
rail: Removal - Refitting, 13B-64).
READ NEXT:
K9K, and 750 or 752 or 766 or 768
IMPORTANT
Use the diagnostic tool before any operation is carried
out on the injection circuit to check:
that the injector rail is not under pressure,
that the fu
K9K, and 750 or 752 or 764 or 766 or 768
Note:
Vehicles equipped with the K9K*768 engine may or
may not be equipped with an intercooler.
Disconnect the battery (see Battery: Removal - Refitting)
(
K9K, and 750 or 752 or 766 or 768
To configure the injectors, (see MR 394 Fault finding,
Diesel Injection, Configuration and programming).
Diesel injector: Removal - Refitting
K9K, and 764 or 772
SEE MORE:
JH3 or JR5 or TL4, and CRUISE CONTROL - JH3 or JR5 or TL4, and VEHICLE
WITH CARD
REMOVAL
I - REMOVAL PREPARATION OPERATION
Remove:
the driver side dashboard lower trim clips (1),
the driver side dashboard lower trim (2).
II - OPERATION FOR REMOVAL OF PART
CONCERNED
CRUISE CONTROL
Dis
This system enables a reduced fuel
consumption and lower greenhouse
gas emissions. The system is activated
automatically when the vehicle is
started. While driving, the system stops
the engine (standby) when the vehicle
is at a standstill (traffic jam, traffic lights,
etc).
Conditions for en